New York
CNN
—
President Donald Trump has said that automakers can avoid his tariffs by simply moving production to American plants. But it’s not that easy. Not by a long shot.
A wide variety of tariffs have either already hit, or are about to hit, the auto industry, potentially adding thousands of dollars to the cost to build and buy a new car. Duties of 25% on steel and aluminum imports went into effect this week, and levies on cars from Asia and Europe are set to go into effect next month. Perhaps most damaging to automakers, import taxes on all goods, including cars and parts imported from Canada and Mexico, have been announced – and put on hold – twice since Trump took office, and are set to be put in place once again in April.
The Trump administration has listened to pleas from automakers to spare them from tariffs, and said there’s an easy answer – just build cars in the United States.
“He told them they should get on it, start investing, start moving, shift production here to the United States of America, where they will pay no tariff,” White House Press Secretary Karoline Leavitt said earlier this month, after Trump delayed tariffs on most Canadian and Mexican goods from taking effect for a month. “That’s the ultimate goal.”
Although the administration suggests such a shift can be accomplished quickly – and without a downside – that’s far from the truth.
‘A lot of costs, and a lot of chaos’
While automakers are seeing “a lot of cost and a lot of chaos” from Trump’s tariff threats, as Ford CEO Jim Farley said in comments at an investor conference last month, they’re still not going to build new plants, at least not immediately.
Part of that is because Trump’s on-again-off-again policies on tariffs doesn’t provide the certainty that automakers need to invest billions of dollars in new plants.
“If they become permanent, then there’s a whole bunch of different things that you have to think about, in terms of where do you allocate plants, do you move plants, etc.,” General Motors CFO Paul Jacobson told investors last month.
But he said the company has too many questions about the future of trade policy to make those kinds of decisions.
“Those are questions that just don’t have an answer today,” he said. “As much as the market is pricing in a big impact of tariffs and lost profitability, think about a world where we’re spending billions in capital, and then it ends. We can’t be whipsawing the business back and forth.”
That’s despite the punishing costs of tariffs. Although the steel and aluminum tariffs won’t raise automakers’ immediate costs thanks to long-term contracts with suppliers, future costs likely will, even if they buy from American producers, since those suppliers will be able to raise prices.
Both General Motors and Ford estimated increased commodity costs following Canadian steel and aluminum tariffs put in place in 2018 cost them more than $1 billion each. American steel prices are already up 30% or more in the last two months, according to Phil Gibbs, steel analyst for KeyBanc, and aluminum prices are up about 15%.
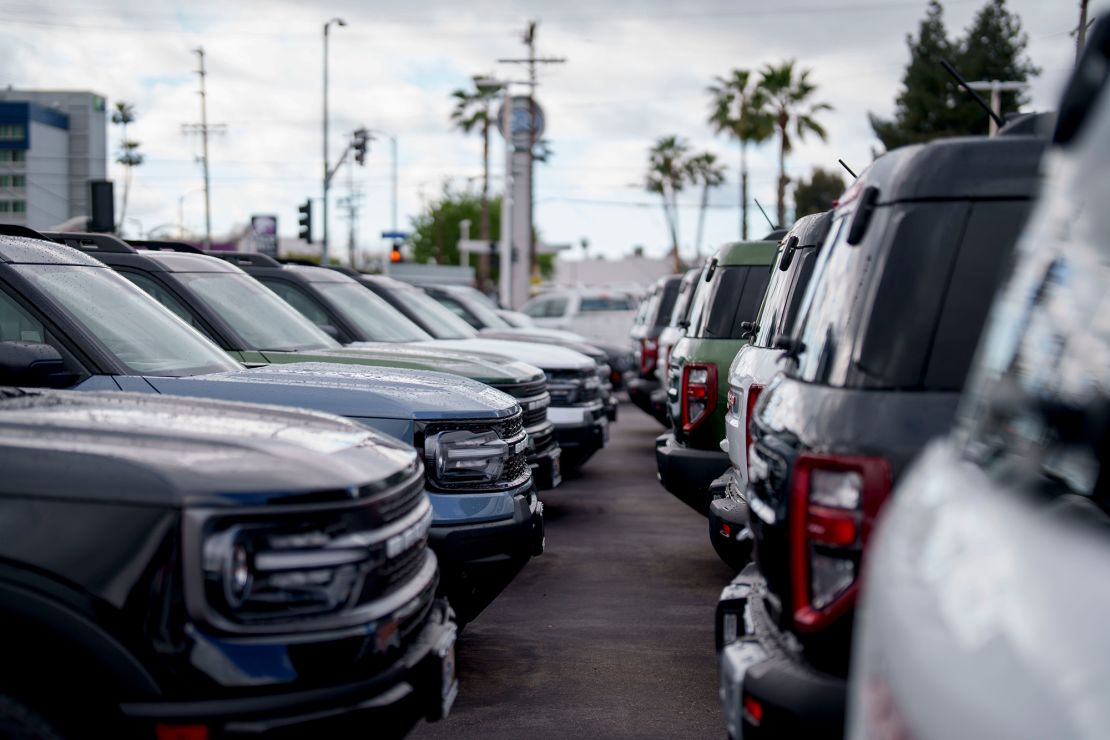
Even something as seemingly simple as switching a factory to a different model in the lineup can shut the plant down for a year or more. It also takes years for an automaker to go from announcing a new factory to the first car rolling off the assembly line. That’s even in the case of a closed plant that is being reopened.
Stellantis, which makes cars in North America under the Jeep, Ram, Dodge and Chrysler brands, agreed to re-open a shuttered plant in Belvidere, Illinois, as part of the deal to end a 2023 strike by the United Auto Workers.
It pointed to those re-opening plans once again in January, soon after Trump took office, to assure him it would increase American car production. But that plant won’t reopen until 2027.
And despite Trump’s argument that his tariff threats are needed to “save” the US auto industry, US factories already produce the lion’s share of North American auto production.
According to data from S&P Global Mobility, there were 10.2 million cars built at US assembly plants last year, compared to 4 million at Mexican factories and 1.3 million in Canada. There are about 1 million workers at American factories producing cars, trucks and auto parts.
And about half of the cars built in the United States are made at so-called “transplants” operated by Asian or European brands, such as Toyota, Honda, BMW and Volkswagen. That’s not because of tariffs, but because there are significant costs involved with shipping autos across oceans, so it makes sense to build them close to where they’re going to be sold.
Some of the models built in Mexico are lower priced models, like the Jeep Compass or Ford Bronco Sport, that have thinner profit margins than larger, more expensive vehicles built at US plants. Producing those vehicles at American plants using higher paid workers, or continuing to build them in Mexico and having a 25% tariff slapped on them, could raise the cost so much that there would be no demand those models. So the automakers might decide to stop offering them altogether.
If that happens, it not only would reduce the options for car buyers looking for an affordable new cars, it could cost American jobs, since even the cars built in Mexico have American-made parts. For example, some of the Ford Bronco Sports built in Mexico have an American-built engine.
But even if the automakers open new factories, or increase production at existing plants, it won’t stop tariffs from raising the cost of “American” cars by between $3,000 to $12,000 per vehicle, according to an estimate from the Anderson Economic Group, a Michigan-based think tank.
That’s a cost that would be passed onto dealers, who buy vehicles wholesale, and eventually onto car buyers, making cars that are already near record high prices unaffordable for many buyers, or unprofitable for the automakers to continue to build. So the result would likely be less production, and fewer jobs building cars and parts.
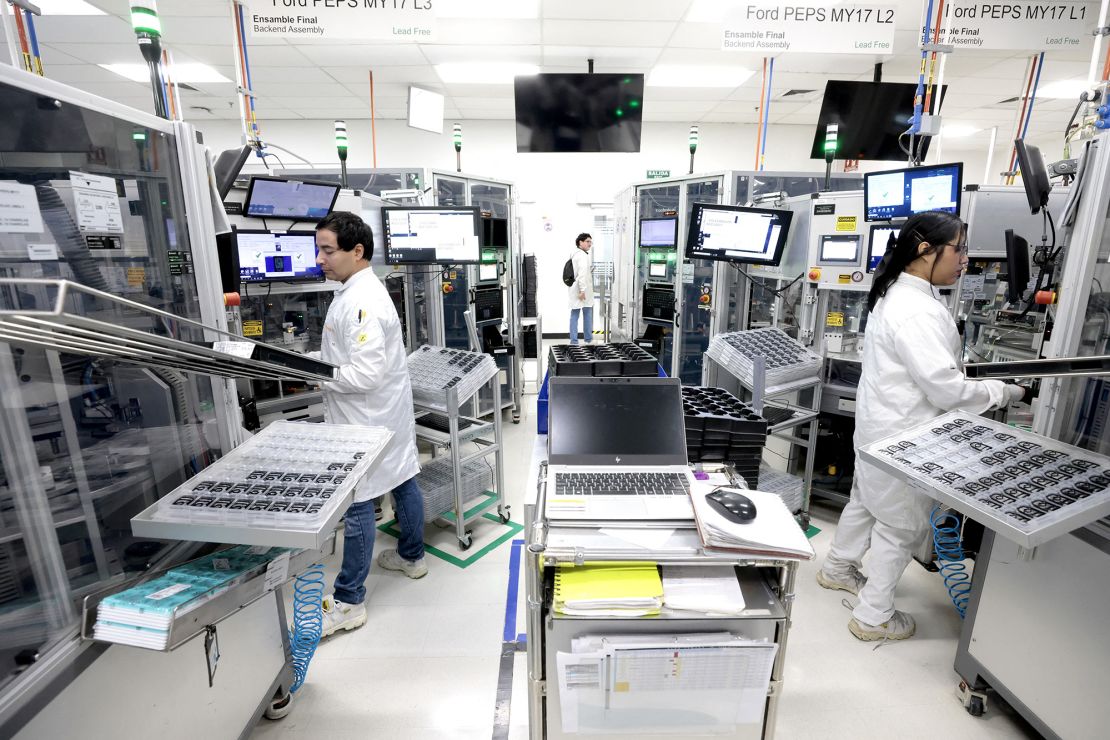
Automakers have been operating for decades as if North America is a single market, first under NAFTA and then under the successor trade deal negotiated by Trump during his first time, the US-Mexico-Canada trade deal, or USMCA. Under those rules, the automakers moved parts freely across the borders, sometimes several times, on their way to final assembly.
Mexico exports $82 billion worth of auto parts to the United States, most of that going to automakers to be used in their assembly plants. That’s 70% more than the value of the passenger cars Mexican plants ship to US dealerships. Canada auto parts exports came to $19 billion last year.
But the US parts manufacturers, which employ more than twice as many workers as the 300,000 who work in US assembly plants, ship $36 billion in parts to Mexico and $28 billion to Canada. If those shipments stop in the near term due to tariffs, it could cost hundreds of thousands of American jobs.
The movement of parts back-and-forth across the border means is no such thing as an all-American car. The US government tracks what percentage of each car’s parts is made “domestically.” But under USMCA both Canadian-made parts and US-made parts are counted as the same domestic content. Even with the broader definition of “American made,” none exceed 75%.
Trump insists that automakers are already making plans to open up new US auto plants.
“We’re going to have growth in the auto industry like nobody’s ever seen — plants are opening up all over the place,” he said in his recent address to Congress.
“Numerous car companies have announced that they will be building massive automobile plants in America, with Honda just announcing a new plant in Indiana, one of the largest anywhere in the world,” he added.
The plants now under construction are partly funded with federal assistance from the Inflation Reduction Act, the green energy bill passed during the Biden administration that Trump has made clear he wants to see rolled back.
Honda has also had a plant in Indiana since 2008. Reuters reported last week that Honda had dropped plans to build the next generation of Honda Civic in Mexico and would continue to build it at Honda’s existing plant in Indiana. It cited three people in Japan familiar with company plans for that report, which said the threat of tariffs on Mexican exports to the United States was the reason for the change of plans.
Honda also would not confirm nor comment on that report.
What’s clear is that automakers would have significantly less cash to build any new facilities should tariffs upend the industry.
“Let’s be real honest: Long term, a 25% tariff across the Mexico and Canada borders would blow a hole in the US industry that we’ve never seen,” Ford’s Farley said in his recent comments to investors.